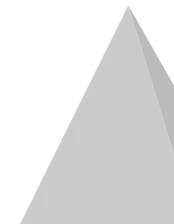
Tetra In Action - May, 2016
Managing the Power Piping in CCGT Plants Risk of failure and attendant personnel safety concerns are always present when operating highly-pressurized systems.
Tetra Engineering announces a series of targeted workshops to provide thermal and process plant O&M engineers, managers and operators with a working knowledge in several aspects of the boiler and steam process technology. Drawing on our field experience working at power and process plants throughout the world, the objective is to provide attendees with clear instruction on the operator actions and design issues that can impact reliability, efficiency and operating life. The programme comprises a set of focused, half-day training modules intended to leave attendees with a practical working knowledge on these issues. A number of outside experts will join Tetra's senior staff in delivering the workshops.
An engineering consultant needs to stay up to date in his knowledge and try to contribute to furthering that knowledge. Therefore, the staff engineers at Tetra don’t just work on commercial projects, they also take the time to do research and development on a variety of boiler and steam cycle engineering issues. This is actively encouraged by the company as it only increases the level of skill that our collaborators can bring to bear for solving a given client’s problem.
Over the years Tetra engineers have published many papers and attended numerous technical conferences and forums. In the past 2 years the following papers were presented or published with collaborators from the various Tetra offices as authors or co-authors:
An additional paper by Tetra collaborators Dave Moelling and Andreas Fabricius (and third co-author Jan Rusaas of R&R Consult) has been accepted for presentation at the upcoming Powergen Asia (Tuesday Sept 20th, see details here): Root Cause Failure Analysis of Superheater Tubes Using Computational Fluid Dynamics Simulations.
HRSG Structures are exposed to weather, hot turbine exhaust gases, steam and water leaks and emissions control chemicals. Deadweight, wind, thermal and seismic stresses also are applied to the HRSG. These components are typically inspected on an opportunistic basis, for example during annual statutory inspections by the insurance company’s boiler inspector or during scheduled work on other major components such as the GT.
Early HRSGs had frequent problems with the duct and casing/liners. HRSG OEMs have responded to these problems with improved rials, improved bolting patterns and related improvements to designs of other components such as duct burners that have been responsible for damage to liners in certain configurations.
Casing liner plates are often found damaged in the transition duct at the exit of the gas turbine. This is particularly common in ducts with abrupt geometry changes such as 90° angles in the duct or other sharp angled transitions. Another common location for liner damage…
Stay up to date and refer to our large collection of technical white papers and articles
Managing the Power Piping in CCGT Plants Risk of failure and attendant personnel safety concerns are always present when operating highly-pressurized systems.
Read about our latest training course, our HRSG Inspection Planning Guide and a World Record set by one of our employees...
Read about our Managing Boiler & Steam Cycle Pressure Part Integrity training, our Covered Piping System Maintenance Programme and a World Record...
Grade 91 Damage Detection methods HRSG Inspections. Planned, periodic inspection of HRSG and associated steam cycle Balance of Plant is an essential component of a plant maintenance regime.