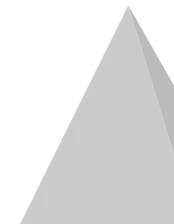
Remote Visual Inspection (RVI), or Borescope
One of the first applications of the borescope was for inspecting steam turbine rotor discontinuities in the 1...
The borescope is an essential tool for inspecting of power plant components. Commonly used in high-value rotating power-plant equipment such as steam turbines, gas turbines and generators it is also extremely useful for checking the internal or to reach external surfaces of boiler and HRSG tubes and piping.
The borescope inspection (also known as a "remote visual inspection" or RVI) involves using a flexible or rigid optical device that allow the inspector to examine areas that are otherwise difficult to access. Early borescopes were a simple tube, whereas today even basic models are equipped with cameras (and usually) lighting at the end of the viewing probe. More expensive models include articulated heads and higher-quality optics.
The choice of hardware is to some extent dependent on the application, a lower-end scope without articulation is often sufficient for checking larger diameter pipes.
In the context of a boiler, which is a closed vessel that generates heat through the combustion of fuel, a borescope inspection can serve several purposes:
During a borescope inspection, a trained technician or engineer inserts the borescope through a small access port or opening in the boiler's casing. The borescope's camera provides real-time images of the internal components on a screen, allowing the inspector to assess the condition of various parts. The inspection process can be recorded for later analysis and reporting.
It's important to note that borescope inspections require proper training, safety measures, and equipment to ensure the well-being of inspectors and the integrity of the equipment being examined. If you're considering a boiler borescope inspection, it's recommended to consult with professionals who specialize in boiler maintenance and inspection to ensure the process is carried out effectively and safely.
Stay up to date and refer to our large collection of technical white papers and articles
We’re pleased to announce that our presentation on the “Application of Artificial Intelligence to Boiler Tube Failure Analysis” has been officially accepted for the upcoming Institution of Mechanical Engineers (IMechE) - Boiler User Group 2025.