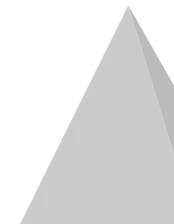
2018 CPS Piping Services for CCGT Plants
2018 CPS Piping Services for CCGT Plants Tetra Engineering Group, Inc.has assistedmany owners of natural gas-fired combined cycle plants with the development of effective Covered Piping Systems (CPS) Programs, Inspection Plans, Pipe Stress Analysis and Field NDT since the ASME adopted the new Code requirements for piping O&M in Section B31.1 Chapter VII in 2007. Tetra has developedsuch programsfor CCGT owners in the US, Canada, Mexico and the Middle East. They have been prepared for 'bubble' 2x1 design with F-class gas turbines as well as modern 1x1 fast-start units, plants with aeroderivative GTs and once-through steam generators as well as smaller units operated by municipal power companies, some of which are in cogeneration service. Based on the latest B31.1 requirements, the CPS Program Plan is tailored to meet your requirements especially regarding the scheduling of NDT inspections over multiple outages to distribute costs and meet outage budget constraints Covered Piping systems O&M Programs for CCGT Plants