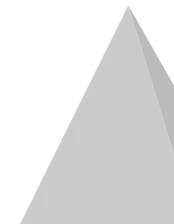
Thermal Plant Simulation
How a High Fidelity Thermal Plant Simulation Package Can Help Your Engineering Group Keep Your Plants at Peak Productivity?
Tetra Engineering, in collaboration with R&R Consult, has successfully resolved a critical performance issue at a 1509 MW natural gas-fired power plant using advanced Computational Fluid Dynamics (CFD) analysis. The problem revolved around a Heat Recovery Steam Generator (HRSG) that failed to produce the expected amount of steam, subsequently reducing the plant’s electricity output.
The HRSG is a crucial component in power plants, functioning as an energy recovery heat exchanger that captures heat from hot gas streams, such as those from a combustion turbine, to generate steam. This steam is vital for various industrial processes and for driving steam turbines to produce electricity.
During an inspection, it was discovered that a significant volume of hot flue gas bypassed the boiler tubes, flowing instead along the sides of the boiler and through two central bypasses between three individual modules. This bypass was suspected to be the main cause of the reduced steam production.
To investigate, R&R Consult conducted a CFD analysis of a single HRSG module. The results revealed areas with accelerated bypass flow, identified as red zones in the velocity distribution model. The temperature distribution analysis further confirmed that the bypassed exhaust gas passed through the module with minimal heat transfer.
The CFD simulation provided a detailed velocity and temperature distribution, highlighting the extent of the bypass flow. The analysis concluded that an average of 6.3% of the exhaust gas bypassed the boiler tubes, leading to insufficient heat transfer and reduced steam production.
With these insights, Tetra Engineering performed a thermal analysis to verify the impact of the bypass flow on the HRSG’s performance. The analysis confirmed that the bypass flow was indeed the primary cause of the decreased steam output. Consequently, plans were made to install covering plates to minimize the bypass flow.
The installation of covering plates at strategic locations, such as the side walls and the center of the modules, effectively addressed the issue. This solution was directly informed by the CFD analysis, underscoring its significant role in identifying and resolving the problem.
For further details, please contact:
Stay up to date and refer to our large collection of technical white papers and articles
How a High Fidelity Thermal Plant Simulation Package Can Help Your Engineering Group Keep Your Plants at Peak Productivity?
Tetra Engineering provides a full-scope service for the modelling and operation analysis of all types of natural or forced circulation Power Boiler and HRSGs, including supercritical and once-through designs.
Many combined cycle power plants have experienced thermal shock damage to bypass power piping, especially in the HP steam and Hot Reheat systems.