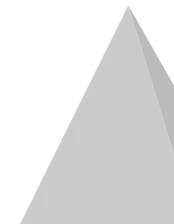
GT Upgrade Effects on HRSG Pressure Parts
Tetra Engineering Group, Inc. (TETRA) has assisted the owners of natural gas-fired combined cycle plants with ...
As your Heat Recovery Steam Generator (HRSG) advances in service life, it is advisable to assess the replacement of pressure components. This proactive evaluation aims to fortify the structural integrity of your unit, mitigate operational and maintenance costs, and extend the overall operational lifespan of the plant.
As your Heat Recovery Steam Generator (HRSG) advances in service life, it is advisable to assess whether some of the components that make up the pressure boundary may need replacing. The objective is to assure the structural integrity of the unit for the remaining design/operating life, or to eventually extend that life if desired, while minimizing disruptions and future O&M costs.
The first step in the process of deciding on pressure parts replacement is to perform a detailed engineering assessment. As performed by Tetra Engineering, it provides a sound basis for decisions on pressure part replacement by delivering a detailed evaluation of the condition of the components, the operational risks in keeping or replacing and if requested, a Front-End Engineering Design (FEED) study.
Tetra Engineering can support in the engineering of new pressure parts through two different approaches.
In the first case, Tetra Engineering can provide guidance on design changes such as specifying different grades of material (to resist FAC for example) or layout (to improve performance in a cycling regime)
Tetra Engineering provides field support and supervision during the installation & fabrication of the new pressure parts.
Tetra Engineering can provide an engineering review of commissioning procedures as well as on-site support to witness the commissioning activities such as hydrotesting.
Tetra Engineering has been supporting clients with their pressure part replacements since 2010 and has been involved in all parts of the process.
Tetra Engineering also has an extensive network of partners who can support in different aspects of the process, including specialisation in the Asian supply Market.
We can tailor our services to your needs
Stay up to date and refer to our large collection of technical white papers and articles
We’re pleased to announce that our presentation on the “Application of Artificial Intelligence to Boiler Tube Failure Analysis” has been officially accepted for the upcoming Institution of Mechanical Engineers (IMechE) - Boiler User Group 2025.